Conférence présentée par
Patrick Arnaud, ancien président,
Iann Bouchard, directeur de la communication de Winoa,
avec la participation de Christophe Bertoncelli, directeur des opérations
lundi 11 mars 2024
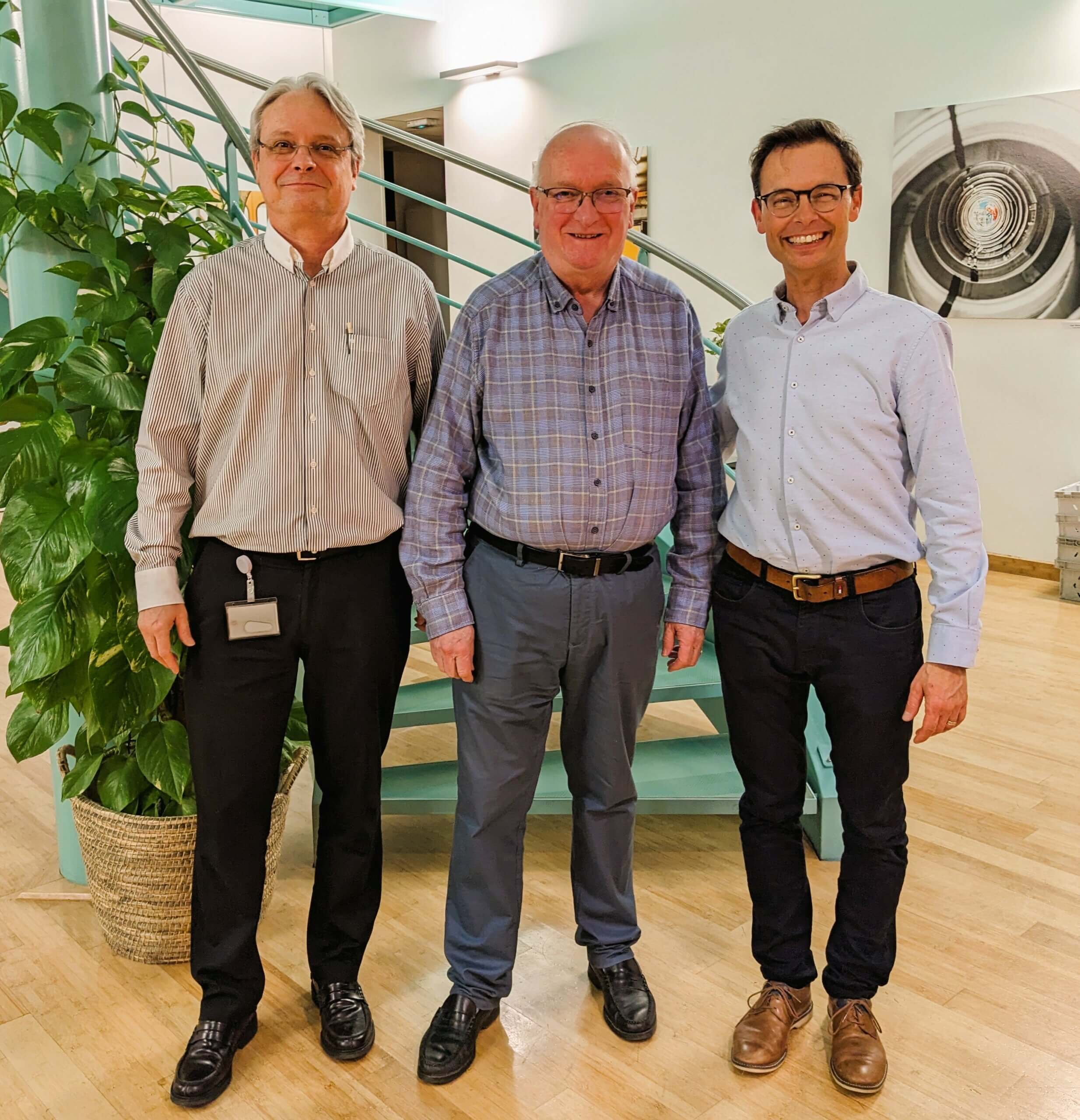
Compte rendu de la Conférence
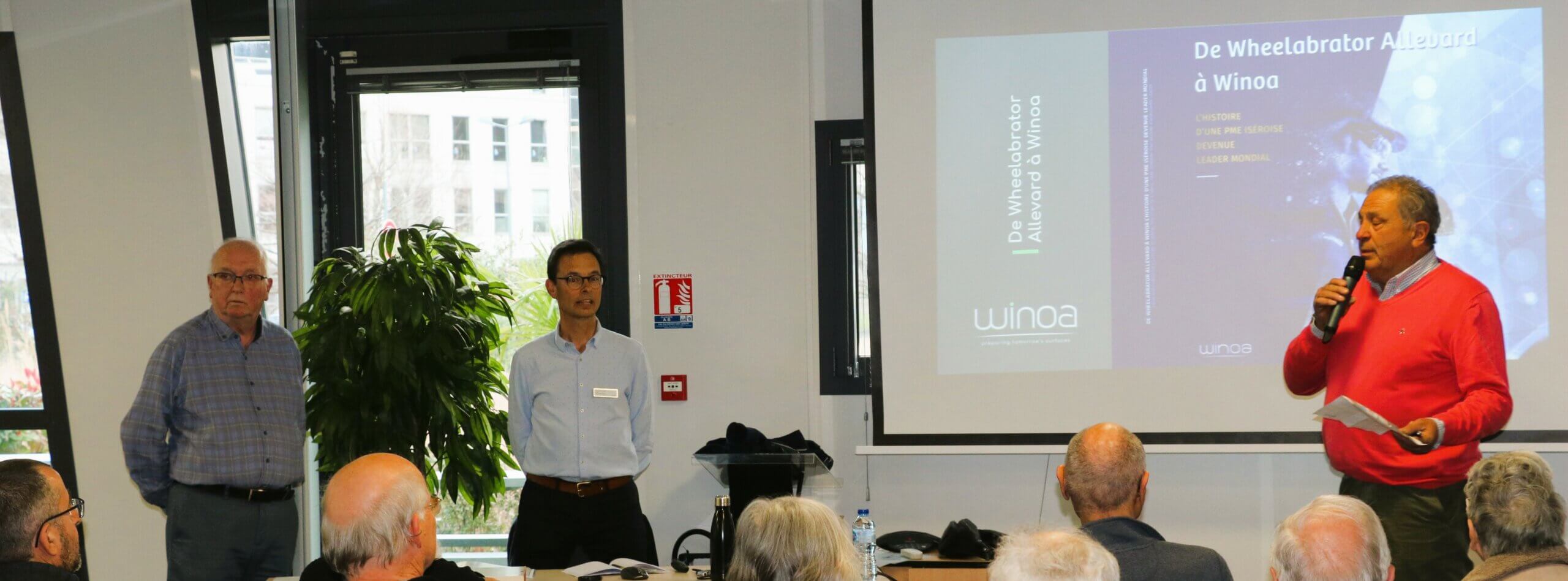
Résumé de la Conférence
par Anne Laffont
(Crédit photos : merci à Winoa pour les photos fournies pour illustrer cet article)
La conférence commence par une vidéo (disponible sur youtube) et la description de la fabrication de la grenaille, cœur de métier de Winoa (« Préparons les surfaces de demain ») et de Patrick Arnaud qui y a travaillé de 1977 à 2017.
- On part de ferraille (95% sont des métaux recyclés, Winoa est un gros recycleur, et 100% de ce qui est produit est recyclable)
- Un jet d’acier liquide (four à arc) est balayé par un jet d’eau (atomisation) avec formation de petites billes.
- Les billes non sphériques ou de trop grande taille sont broyées pour former la catégorie des angulaires.
Pour commencer, Patrick Arnaud met en avant deux personnages :
- Aristide Bergès qui utilise en 1867 l’énergie hydraulique (turbine d’une puissance jusqu’à 1500 chevaux) pour faire fonctionner ses défibreurs.
- Le général Benjamin Chew Tilghman qui a découvert en 1869 le sablage (et dépose un brevet), puis la grenaille pour remplacer le sable dans la préparation de surface (le sable pouvait rester collé). Il a inventé l’atomisation de la fonte (point de fusion plus bas) à partir d’un rouleau horizontal.
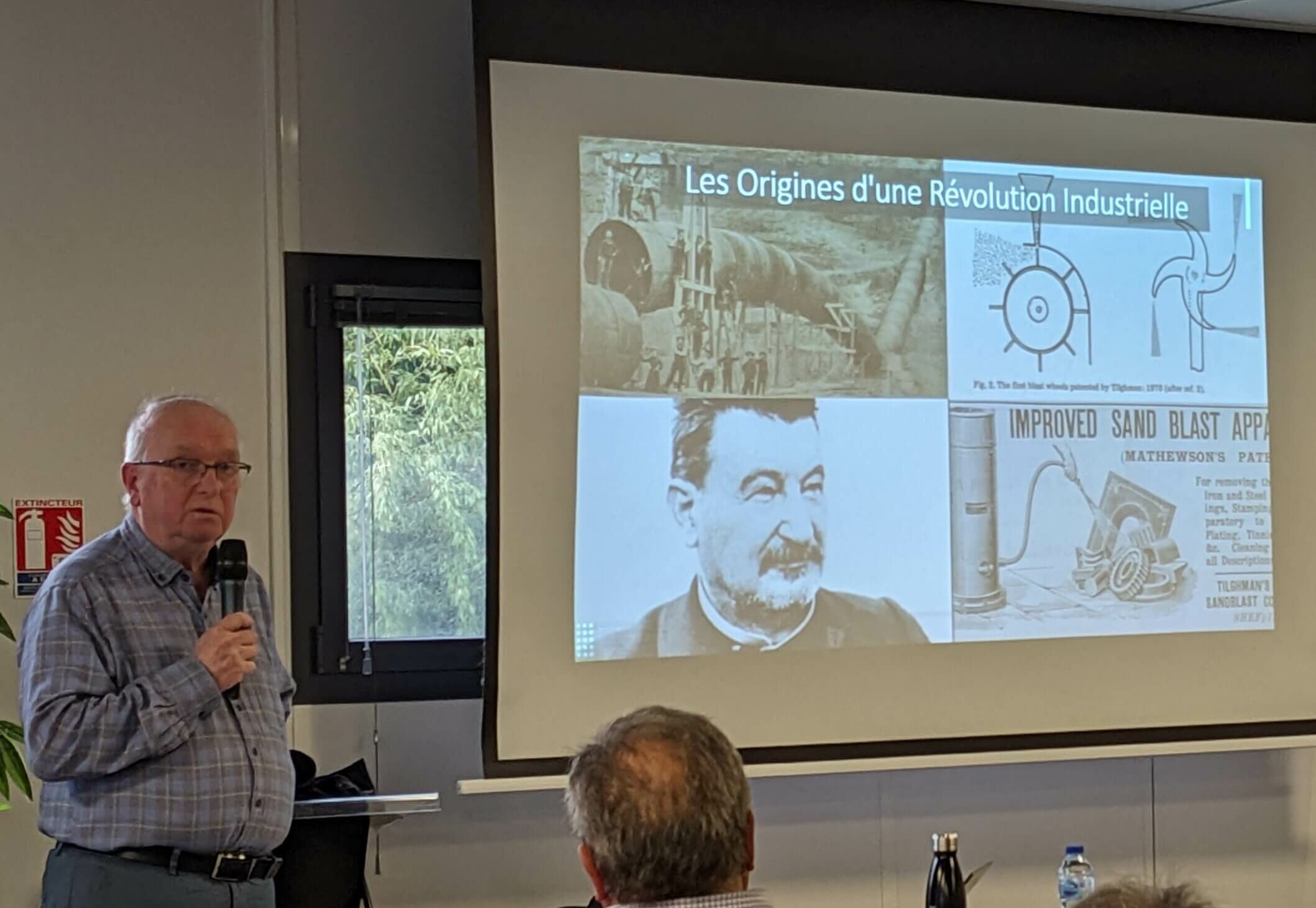
Aux Etats-Unis, vers 1930 Louis D. Peik construit une turbine pour fabriquer la grenaille. De là vient le terme « Wheelabrator ».
En 1960 aux USA la vision devient mondiale. La société Bell Intercorp Group (actionnaire de Wheelabrator) devait suivre. De là, trois partenariats sous licence :
- Avec l’usine anglaise pour couvrir l’Europe du nord (Tilghman Wheelabrator)
- Avec le groupe des forges d’Allevard (qui produisait de l’acier) pour l’Europe de l’ouest (c’est Pierre Baylot, le seul qui parlait à peu près l’anglais, qui a rencontré la société américaine). Avec des centrales sur le Breda, les forges avaient de l’électricité à revendre. Wheelabrator Allevard sera 49% français et 51% US.
- Au Japon (pour couvrir l’Asie, le Brésil) un deal similaire avec Sinto.
En 1961 est construite l’usine de fabrication de grenaille au Cheylas, avec le transfert de tout le know-how, ainsi que l’assistance commerciale de Wheelabrator US. La production avec un four de 2t de capacité est alors de 8000 tonnes par an, et le four est saturé en 5 ans. Un nouveau four de 4t est installé en 1967 et la capacité monte alors à 26 000 tonnes par an, puis un autre de 15t en 1971.
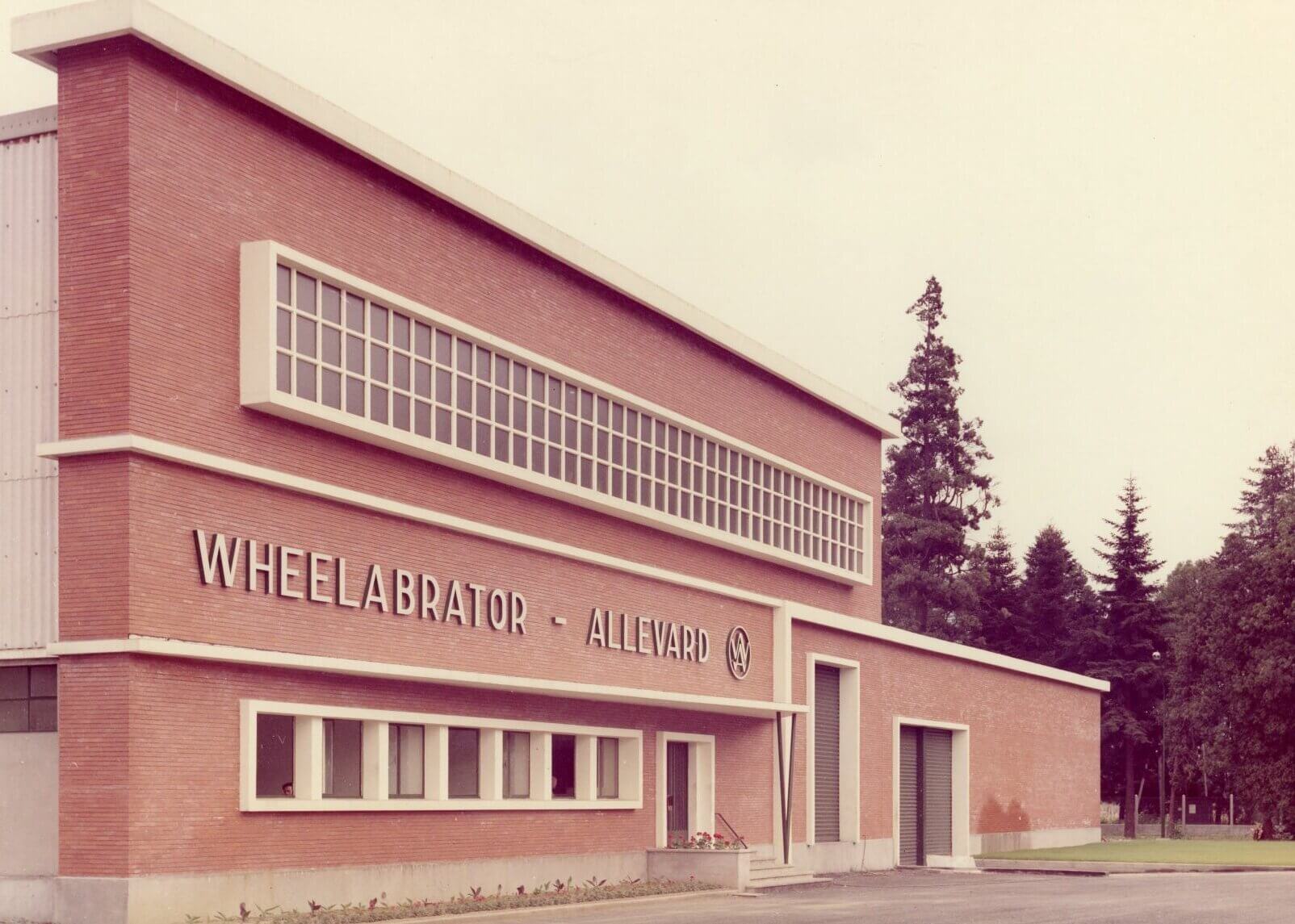
Wheelabrator Allevard a su saisir des opportunités pour sa croissance externe :
- En 1980, Wheelabrator Allevard achète la filiale anglaise de Bell Intercorp (qui avait décidé de ne pas poursuivre, la licence ayant été signée pour 20 ans).
- Un nouveau marché apparaît, celui de la découpe de pierre de granit (1000 à 2000t/an). En rentrant sur ce marché, la concurrence est affaiblie (supériorité de la grenaille acier vs fonte) et Wheelabrator Allevard rachète l’italien Abrasivi. Dès lors, 50% de sa production est dédiée au granit.
- Rachat d’usines d’Europe de l’Est et prise du contrôle du marché de l’Est après la chute du mur
- Autre opportunité dans les années 90 : Bell Intercorp qui passe à autre chose si le métier stagne, cède sa participation à Wendel.
- Au Japon il y a deux producteurs : Sinto et IKK (Itoh Kikoh). IKK a fait faillite suite à la crise bancaire asiatique. Wendel lui rachète les parties Brésil, Thaïlande et une partie du Japon. Wheelabrator Allevard se retrouve alors en concurrence avec Sinto.
- Rachat d’une usine espagnole basque (licence d’Ervin, société américaine qui rachète l’usine anglaise, ce qui permet à Wheelabrator Allevard d’acheter l’usine basque) .
Wheelabrator Allevard a toujours été soutenu dans ses projets industriels par la famille Wendel. Mais avec ses 600 héritiers, un duo de choc est embauché. En 2005 Wheelabrator Allevard est vendu à LBO France, fonds d’investissement, pour 410 M€ (en 1982 la valeur était de 5 à 10M€). Il en découle un changement de stratégie : ce n’est plus la même mentalité industrielle.
En 2011, pour ses 50 ans, la société est rebaptisée Winoa.
En 2024, Sinto (société cotée) rachète Winoa : cela revient à recréer la société telle qu’elle était avec les américains.
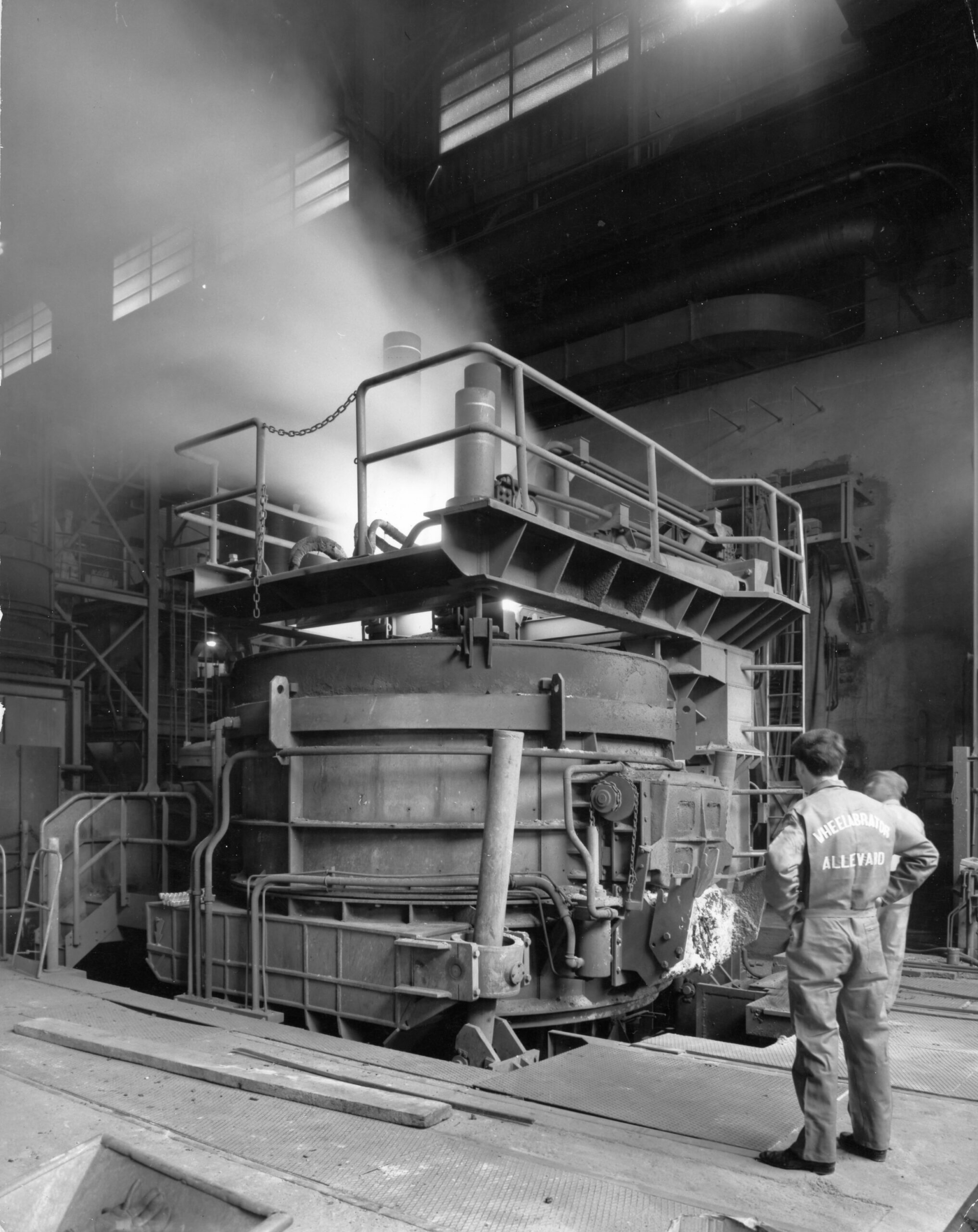
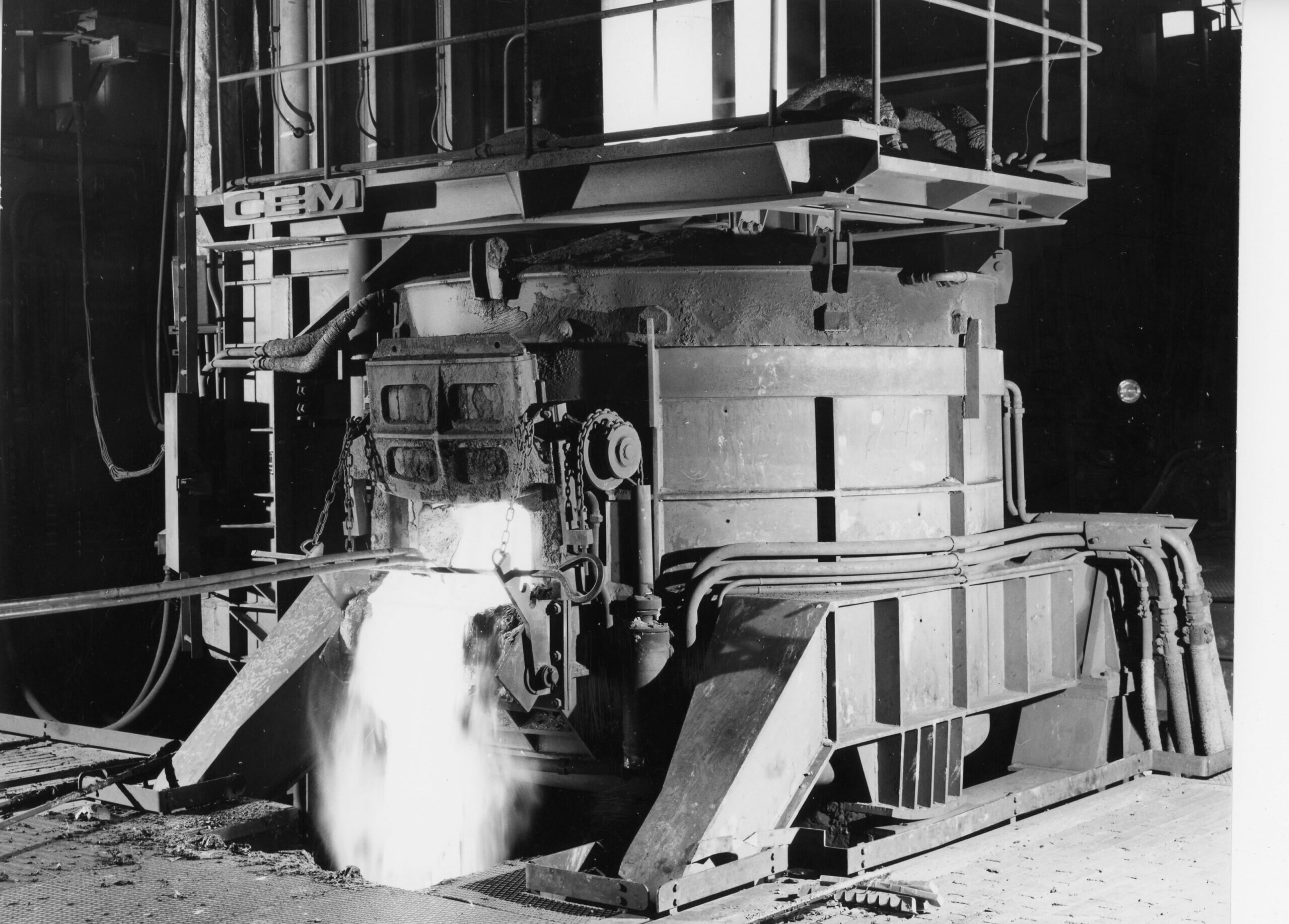
Iann Bouchard, en France depuis deux ans et demi, prend le relais pour conclure cet exposé.
Les défis de Winoa :
- Le fil diamanté a remplacé la grenaille pour la découpe du granit
- Le portefeuille change (acier, inox, fil coupé), la vente en ligne se développe.
- La feuille de route environnementale :
- en 2020 : 300kg de CO2 par tonne de grenaille ;
- objectif pour 2050 : 0%
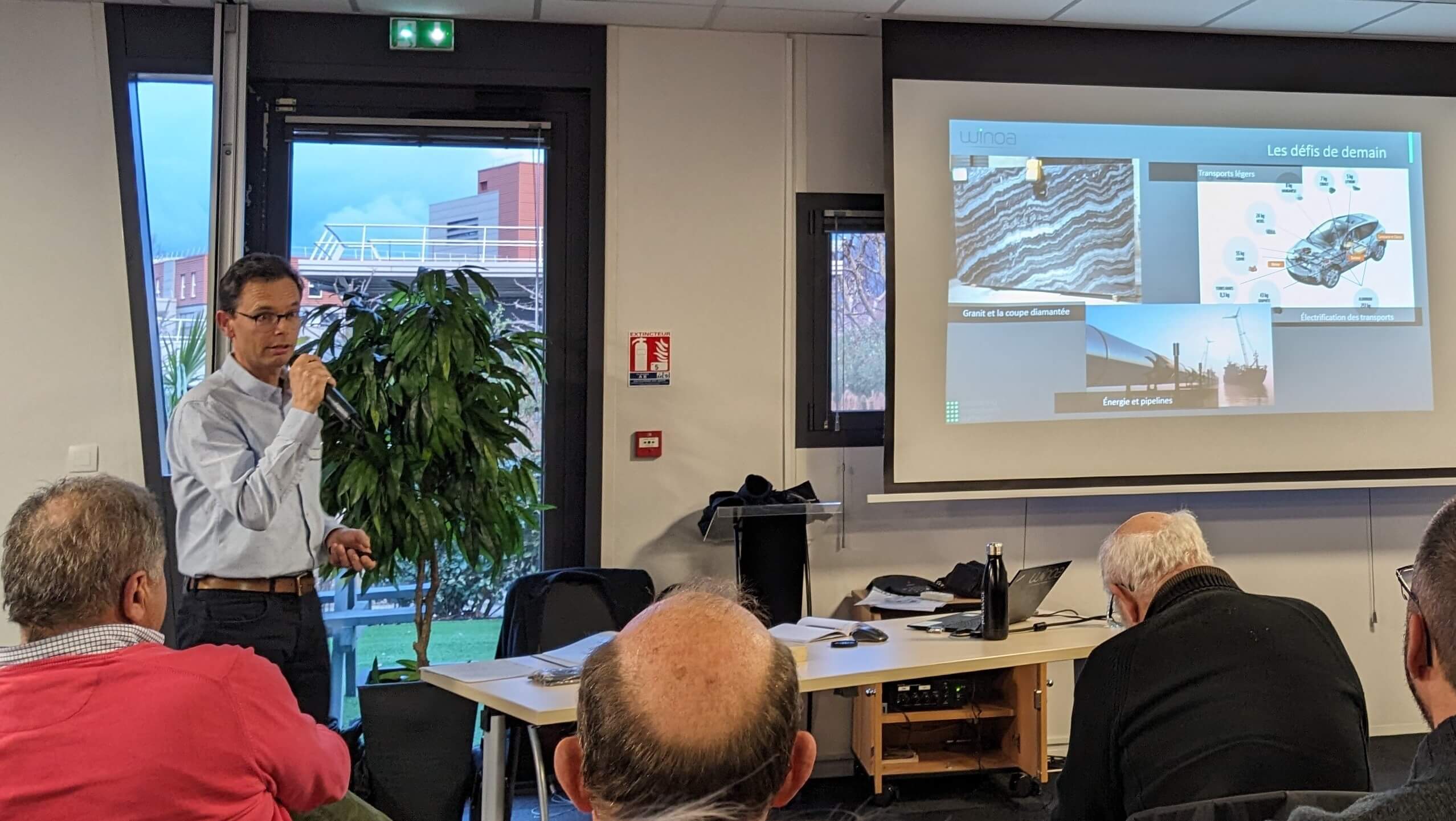
Questions/réponses
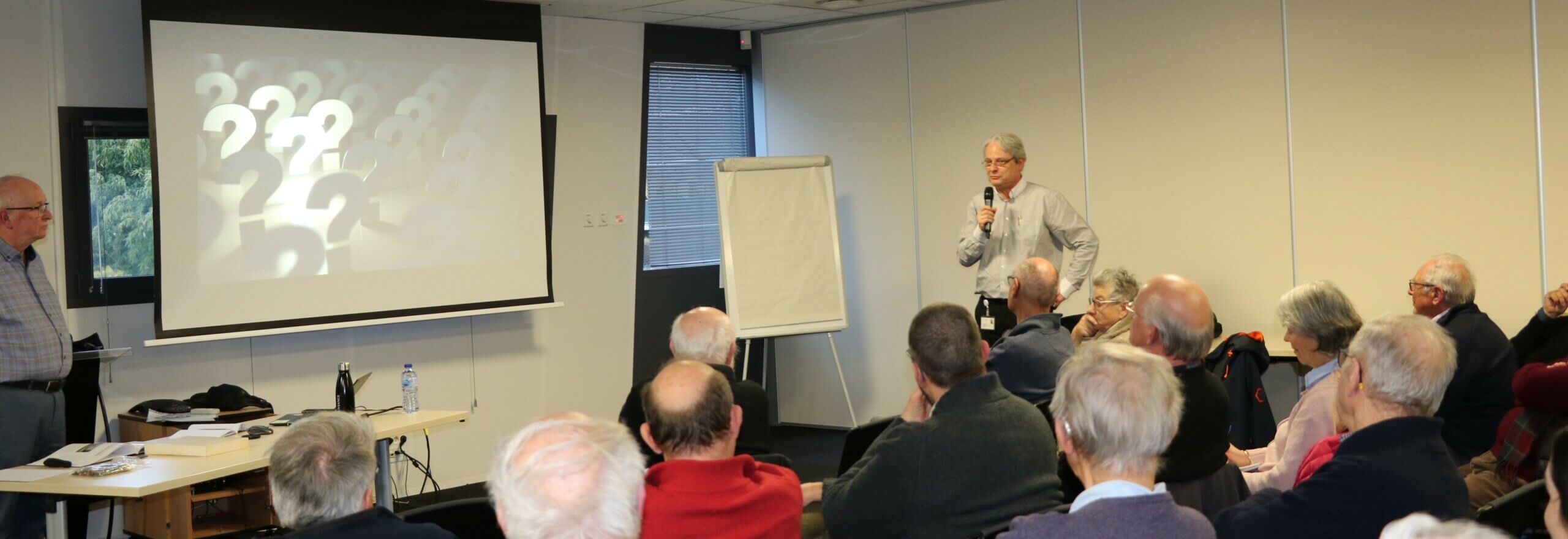
- Que signifie Winoa ? Le nom de Wheelabrator appartenait aux américains. Winoa est la contraction de Wheelabrator Innovations Allevard.
- Quand les américains ont cédé leurs activités, il n’y a pas eu de changement dans la direction.
- Les centrales électriques appartenaient aux forges d’Allevard, et n’ont jamais appartenu à Wheelabrator Allevard.
- La grenaille est récupérée par aimantation. C’est un des inconvénients du sablage, le sable ne peut pas être séparé de la poussière et présente un risque de maladie pulmonaire.
- Si un grand client est proche, la grenaille peut être récupérée par l’usine.
- La grenaille peut rester entre 2000 et 3000 tours dans la grenailleuse avant d’être usée.
- Évolution des effectifs :
- Un millier dans le monde, et 200 en France
- Amélioration de la productivité : Alors qu’il fallait 3h de main d’œuvre pour produire 1t , aujourd’hui 1h suffit.
- Les effectifs de production sont ainsi restés stables, tout en augmentant le volume de production. Les équipes de management ont été renforcées.
- Grains de grenaille :
- Taille entre 0.2 et 2mm, de forme ronde ou angulaire. (la tendance du marché est vers les particules fines)
- Il y a 3 gammes de dureté. Les produits angulaires et durs sont destinés aux pièces à peindre
- Énergie : un contrat EDF n’est plus possible. Il faut ajuster la production sur les périodes où le coût de l’énergie est moindre (planning établi 24 heures à l’avance).
- La grenaille d’acier a remplacé la grenaille de fonte
- Le fil coupé (découpé à la dimension du diamètre par des rouleaux avec des dents) : on utilise des lots de fil rebutés. Le fil coupé a la même fonction que la grenaille
- Le transport se fait par camion.
- Des tentatives de transport par train ont été faites mais il y a trop d’interlocuteurs, et ce qui les intéresse ce sont des trains complets, ce qui n’est pas compatible avec la production telle qu’elle est.
- Dans les années 80, la ferraille était transportée à 60% par wagon et 40% par camion.
- La SNCF client se fait livrer par camion.
Quelques liens pour en savoir plus
- Le groupe Winoa : histoire, stratégie et gouvernance
- L’histoire de Winoa résumée en 3 étapes
- Elements techniques et innovations depuis la création de Wheelabrator
- Benjamin_Chew_Tilghman (Wikipedia)
Un livre a été écrit à l’occasion des 60 ans de la société (1961-2021) : De Wheelabrator à Winoa , histoire d’une PME iséroise devenue leader mondial. La version pdf peut être téléchargée sur le site de Winoa.